Ceramic Blasting Technology: The "Silent Hero" in Enhancing Aerospace Component Performance
In the aerospace industry, the performance of components directly determines the safety and reliability of aircraft. Faced with extreme temperatures, high pressure, corrosion, and other harsh conditions, traditional surface treatment technologies often struggle to balance cleaning efficiency with material protection. Ceramic blasting technology, with its unique process advantages, has emerged as a critical method for boosting component performance. This article explores how ceramic blasting empowers aerospace manufacturing through its technical principles, application case studies, and quality control insights. I. Core Technical Advantages of Ceramic Blasting Ceramic blasting is a process that uses high-speed jets of ceramic particles (e.g., silicon carbide, aluminum oxide) to impact component surfaces. Compared to traditional blasting materials (such as steel grit or quartz sand), ceramic particles offer the following benefits: High Hardness, Low Damage: Ceramic particles achieve Mohs hardness levels of 8–9, efficiently removing oxidation layers, burrs, and contaminants. Their uniform shapes (spherical or polyhedral) minimize substrate scratching. High-Temperature Resistance: Materials like silicon carbide withstand temperatures exceeding 1000°C, making them ideal for treating engine hot-section components (e.g., turbine blades, combustion chambers), significantly enhancing oxidation and thermal shock resistance. Improved Coating Adhesion: Surface roughening via ceramic blasting increases coating adhesion by over 30%, extending the lifespan of thermal barrier coatings (TBCs) and corrosion-resistant layers. Eco-Friendly & Cost-Effective: Ceramic particles can be recycled 5–10 times, reduce dust pollution, and lower long-term costs by 40% compared to traditional abrasives. II. Key Aerospace Applications 1. Engine Hot-Section Component Treatment Aircraft engine turbine blades endure temperatures up to 1700°C and high-speed airflow erosion. Ceramic blasting pre-treatment removes surface oxides and micro-cracks while creating uniform roughness for enhanced bonding of subsequent thermal barrier coatings (e.g., YSZ or rare-earth hafnates). For instance, one turbine blade model saw its coating lifespan increase from 500 to 3,000 hours after ceramic blasting, meeting AS9100 standards for engine durability. 2. Brake System Optimization Aircraft carbon-carbon (C/C) brake discs require high friction coefficients and thermal stability. Precision ceramic blasting (using glass beads or silicon carbide) controls surface roughness (Ra 1.6–3.2 μm), improving friction material adhesion. This boosts braking efficiency by 15% and reduces failure risks caused by surface contaminants. 3. Additive Manufacturing Post-Processing Metal additive manufacturing (e.g., titanium alloy parts) often suffers from residual unmelted powder and layer-step effects that compromise fatigue strength. Multi-angle ceramic blasting efficiently removes residues and smoothens surfaces, increasing component fatigue life by 20–30%. For example, AVIC MTS’s rocket engine electric pump components achieved over 12% high-temperature elongation at 650°C post-treatment. III. Quality Control Priorities Quality managers must focus on these critical factors to ensure process stability: Parameter Optimization: Adjust abrasive size (80–120 mesh), pressure (0.4–0.6 MPa), and angle (30°–60°) based on materials (e.g., aluminum alloys, superalloys) to avoid over-processing. Compliance & Certification: Select ceramic abrasives compliant with AS9100, ISO 9001, and other aerospace standards. Regularly test particle hardness and shape consistency. Surface Inspection: Integrate AI-driven optical scanning or laser profilometers to monitor roughness (Sa/Sz values) and defects in real time, ensuring traceability. IV. Future Trends: From Process Innovation to Material Breakthroughs With the rise of silicon carbide ceramic matrix composites (CMC-SiC) in components like engine guide vanes, ceramic blasting will increasingly integrate with ultra-high-temperature coating technologies. For example, combining blasting with chemical vapor deposition (CVD) to apply ZrC ablation-resistant coatings on CMC-SiC surfaces can triple lifespan in 1700°C oxidative environments. Additionally, smart blasting systems (e.g., robotic path planning) will enhance consistency and efficiency while reducing labor costs. Ceramic blasting is not merely a surface-cleaning tool—it is the "silent engine" driving aerospace component performance. Through precise process control and innovative material pairing, manufacturers can meet stringent industry standards, slash maintenance costs, and strengthen market competitiveness. For quality teams, adopting this technology means gaining an edge in reliability, efficiency, and sustainability.
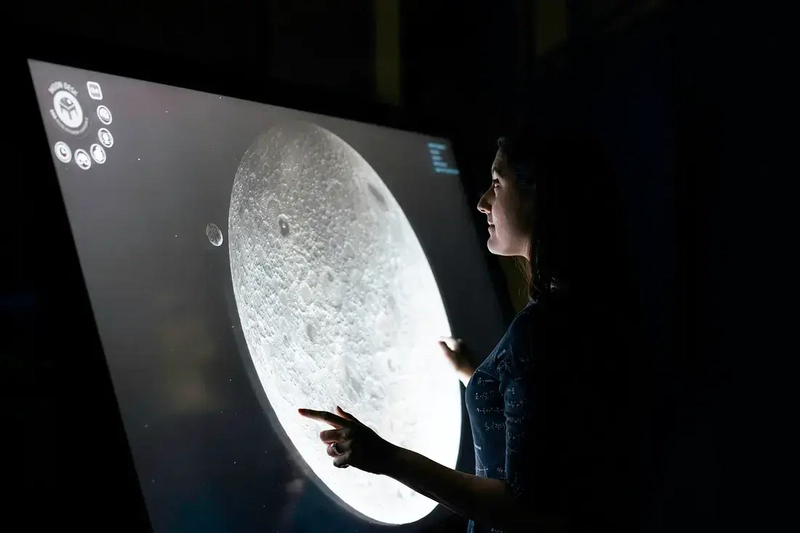
In the aerospace industry, the performance of components directly determines the safety and reliability of aircraft. Faced with extreme temperatures, high pressure, corrosion, and other harsh conditions, traditional surface treatment technologies often struggle to balance cleaning efficiency with material protection. Ceramic blasting technology, with its unique process advantages, has emerged as a critical method for boosting component performance. This article explores how ceramic blasting empowers aerospace manufacturing through its technical principles, application case studies, and quality control insights.
I. Core Technical Advantages of Ceramic Blasting
Ceramic blasting is a process that uses high-speed jets of ceramic particles (e.g., silicon carbide, aluminum oxide) to impact component surfaces. Compared to traditional blasting materials (such as steel grit or quartz sand), ceramic particles offer the following benefits:
High Hardness, Low Damage: Ceramic particles achieve Mohs hardness levels of 8–9, efficiently removing oxidation layers, burrs, and contaminants. Their uniform shapes (spherical or polyhedral) minimize substrate scratching.
High-Temperature Resistance: Materials like silicon carbide withstand temperatures exceeding 1000°C, making them ideal for treating engine hot-section components (e.g., turbine blades, combustion chambers), significantly enhancing oxidation and thermal shock resistance.
Improved Coating Adhesion: Surface roughening via ceramic blasting increases coating adhesion by over 30%, extending the lifespan of thermal barrier coatings (TBCs) and corrosion-resistant layers.
Eco-Friendly & Cost-Effective: Ceramic particles can be recycled 5–10 times, reduce dust pollution, and lower long-term costs by 40% compared to traditional abrasives.
II. Key Aerospace Applications
1. Engine Hot-Section Component Treatment
Aircraft engine turbine blades endure temperatures up to 1700°C and high-speed airflow erosion. Ceramic blasting pre-treatment removes surface oxides and micro-cracks while creating uniform roughness for enhanced bonding of subsequent thermal barrier coatings (e.g., YSZ or rare-earth hafnates). For instance, one turbine blade model saw its coating lifespan increase from 500 to 3,000 hours after ceramic blasting, meeting AS9100 standards for engine durability.
2. Brake System Optimization
Aircraft carbon-carbon (C/C) brake discs require high friction coefficients and thermal stability. Precision ceramic blasting (using glass beads or silicon carbide) controls surface roughness (Ra 1.6–3.2 μm), improving friction material adhesion. This boosts braking efficiency by 15% and reduces failure risks caused by surface contaminants.
3. Additive Manufacturing Post-Processing
Metal additive manufacturing (e.g., titanium alloy parts) often suffers from residual unmelted powder and layer-step effects that compromise fatigue strength. Multi-angle ceramic blasting efficiently removes residues and smoothens surfaces, increasing component fatigue life by 20–30%. For example, AVIC MTS’s rocket engine electric pump components achieved over 12% high-temperature elongation at 650°C post-treatment.
III. Quality Control Priorities
Quality managers must focus on these critical factors to ensure process stability:
Parameter Optimization: Adjust abrasive size (80–120 mesh), pressure (0.4–0.6 MPa), and angle (30°–60°) based on materials (e.g., aluminum alloys, superalloys) to avoid over-processing.
Compliance & Certification: Select ceramic abrasives compliant with AS9100, ISO 9001, and other aerospace standards. Regularly test particle hardness and shape consistency.
Surface Inspection: Integrate AI-driven optical scanning or laser profilometers to monitor roughness (Sa/Sz values) and defects in real time, ensuring traceability.
IV. Future Trends: From Process Innovation to Material Breakthroughs
With the rise of silicon carbide ceramic matrix composites (CMC-SiC) in components like engine guide vanes, ceramic blasting will increasingly integrate with ultra-high-temperature coating technologies. For example, combining blasting with chemical vapor deposition (CVD) to apply ZrC ablation-resistant coatings on CMC-SiC surfaces can triple lifespan in 1700°C oxidative environments. Additionally, smart blasting systems (e.g., robotic path planning) will enhance consistency and efficiency while reducing labor costs.
Ceramic blasting is not merely a surface-cleaning tool—it is the "silent engine" driving aerospace component performance. Through precise process control and innovative material pairing, manufacturers can meet stringent industry standards, slash maintenance costs, and strengthen market competitiveness. For quality teams, adopting this technology means gaining an edge in reliability, efficiency, and sustainability.