Stainless Steel Diaphragm Valves: A Growing Trend in Industrial Applications
Last week highlighted the rising demand for stainless steel diaphragm valves across various industrial sectors. Nearly every order assembled and tested at our UK facility featured stainless steel components, including a recent shipment of 29 DN25 Weir Type valves with GR97 (PTFE/Viton) diaphragms, ready to meet the exacting requirements of our clients. Since introducing our stainless steel diaphragm valve range at KDV Flow, we’ve seen a global industry shift towards these valves in a broad range of applications. Initially, stainless steel valves were used primarily in aseptic environments, such as pharmaceuticals and food processing. However, their exceptional durability, corrosion resistance, and adaptability have expanded their use to industries like chemical processing, water treatment, and more. This trend is driven by the need for equipment that can reliably withstand aggressive chemicals, extreme temperatures, and harsh conditions, while offering extended service life and reduced maintenance costs. This trend is also influenced by stricter industry regulations requiring high-purity and contamination-free fluid handling solutions. Benefits of Stainless Steel Diaphragm Valves: Superior Corrosion Resistance: Stainless steel’s natural resistance to corrosion makes it ideal for handling aggressive chemicals, caustic substances, and exposure to harsh environments, ensuring reliable performance and longer equipment life. In industries such as marine applications and wastewater treatment, this corrosion resistance significantly reduces the risk of premature valve failure. Enhanced Durability: With robust construction and the ability to withstand both high pressures and extreme temperatures, stainless steel valves offer extended operational lifespans and fewer maintenance requirements, reducing downtime and lowering costs. Compared to plastic or brass alternatives, stainless steel diaphragm valves perform better in high-temperature steam applications and chemically intensive processes. Versatility in Customisation: Our stainless steel diaphragm valves can be customised with a variety of linings—such as PTFE, EPDM, or rubber—to enhance chemical compatibility for specific applications. Additionally, we offer a wide range of actuation options, including pneumatic, electric, and manual, to meet diverse operational needs. This flexibility makes them suitable for applications requiring precision flow control, such as dosing and metering in pharmaceutical manufacturing. Wide Range of Applications: From chemical processing to pharmaceutical production and food and beverage manufacturing, stainless steel diaphragm valves are trusted for their reliability and adaptability. For example, in pharmaceutical production, these valves maintain sterility and prevent contamination, while in chemical plants, they handle aggressive, corrosive substances without compromising performance. Moreover, their role in semiconductor manufacturing is growing, as ultra-pure water systems demand high-precision, contamination-free valve solutions. Addressing Key Industry Questions: What are the two types of diaphragm valves? Diaphragm valves are classified into weir-type and straight-through (full bore) designs. Weir-type valves are better suited for sanitary applications, while straight-through valves are preferred for slurry and high-viscosity media handling. Are stainless steel valves worth it? Yes, stainless steel diaphragm valves offer long-term cost savings due to their durability, corrosion resistance, and minimal maintenance requirements. Their higher initial cost is offset by their extended service life and superior reliability in demanding environments. What is the life expectancy of a diaphragm valve? The lifespan varies depending on usage conditions, but high-quality diaphragm valves can last 10–20 years with proper maintenance. Factors such as operating temperature, pressure, and media type influence longevity, making material selection crucial. What is the disadvantage of a diaphragm valve? While highly effective, diaphragm valves have limitations in high-pressure applications and may require periodic diaphragm replacements. Additionally, they are not ideal for handling extremely viscous or particulate-laden fluids, as these can cause wear on the diaphragm material.
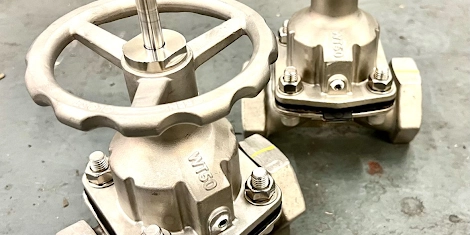
Last week highlighted the rising demand for stainless steel diaphragm valves across various industrial sectors. Nearly every order assembled and tested at our UK facility featured stainless steel components, including a recent shipment of 29 DN25 Weir Type valves with GR97 (PTFE/Viton) diaphragms, ready to meet the exacting requirements of our clients.
Since introducing our stainless steel diaphragm valve range at KDV Flow, we’ve seen a global industry shift towards these valves in a broad range of applications. Initially, stainless steel valves were used primarily in aseptic environments, such as pharmaceuticals and food processing. However, their exceptional durability, corrosion resistance, and adaptability have expanded their use to industries like chemical processing, water treatment, and more. This trend is driven by the need for equipment that can reliably withstand aggressive chemicals, extreme temperatures, and harsh conditions, while offering extended service life and reduced maintenance costs. This trend is also influenced by stricter industry regulations requiring high-purity and contamination-free fluid handling solutions.
Benefits of Stainless Steel Diaphragm Valves:
Superior Corrosion Resistance: Stainless steel’s natural resistance to corrosion makes it ideal for handling aggressive chemicals, caustic substances, and exposure to harsh environments, ensuring reliable performance and longer equipment life. In industries such as marine applications and wastewater treatment, this corrosion resistance significantly reduces the risk of premature valve failure.
Enhanced Durability: With robust construction and the ability to withstand both high pressures and extreme temperatures, stainless steel valves offer extended operational lifespans and fewer maintenance requirements, reducing downtime and lowering costs. Compared to plastic or brass alternatives, stainless steel diaphragm valves perform better in high-temperature steam applications and chemically intensive processes.
Versatility in Customisation: Our stainless steel diaphragm valves can be customised with a variety of linings—such as PTFE, EPDM, or rubber—to enhance chemical compatibility for specific applications. Additionally, we offer a wide range of actuation options, including pneumatic, electric, and manual, to meet diverse operational needs. This flexibility makes them suitable for applications requiring precision flow control, such as dosing and metering in pharmaceutical manufacturing.
Wide Range of Applications: From chemical processing to pharmaceutical production and food and beverage manufacturing, stainless steel diaphragm valves are trusted for their reliability and adaptability. For example, in pharmaceutical production, these valves maintain sterility and prevent contamination, while in chemical plants, they handle aggressive, corrosive substances without compromising performance. Moreover, their role in semiconductor manufacturing is growing, as ultra-pure water systems demand high-precision, contamination-free valve solutions.
Addressing Key Industry Questions:
What are the two types of diaphragm valves? Diaphragm valves are classified into weir-type and straight-through (full bore) designs. Weir-type valves are better suited for sanitary applications, while straight-through valves are preferred for slurry and high-viscosity media handling.
Are stainless steel valves worth it? Yes, stainless steel diaphragm valves offer long-term cost savings due to their durability, corrosion resistance, and minimal maintenance requirements. Their higher initial cost is offset by their extended service life and superior reliability in demanding environments.
What is the life expectancy of a diaphragm valve? The lifespan varies depending on usage conditions, but high-quality diaphragm valves can last 10–20 years with proper maintenance. Factors such as operating temperature, pressure, and media type influence longevity, making material selection crucial.
What is the disadvantage of a diaphragm valve? While highly effective, diaphragm valves have limitations in high-pressure applications and may require periodic diaphragm replacements. Additionally, they are not ideal for handling extremely viscous or particulate-laden fluids, as these can cause wear on the diaphragm material.