KDV Brings You a Wide Variety of Glass-Lined Valves that Shine
Corrosion, wear, and strict hygiene requirements can make industrial operations challenging. That’s where KDV’s glass-lined diaphragm valves come in. Engineered for durability and reliability, these valves are built to withstand aggressive chemicals, abrasive materials, and harsh environments while delivering exceptional performance. Why KDV’s Glass-Lined Diaphragm Valves Outperform Other Types of Valve Not all valves are built to withstand the harsh realities of industrial applications, where exposure to aggressive chemicals, extreme temperatures, and strict hygiene requirements can lead to rapid deterioration. That’s why KDV’s glass-lined valves are the preferred choice for industries demanding long-term performance, reliability, and efficiency. MUST KNOW: Glass is one of the most chemically resistant materials available, impervious to nearly all acids except hydrofluoric acid. This makes glass-lined valves the ultimate defense against corrosion in chemical processing and pharmaceutical industries, where even stainless steel can degrade over time. Longer Lifespans: Glass-lined diaphragm valves significantly outlast traditional valve types in corrosive and abrasive environments, reducing downtime, maintenance costs, and process interruptions. Versatile Across Industries – Our extensive range of glass-lined valves, including the weir-type diaphragm valve, is designed for applications requiring precision flow control, superior corrosion resistance, and strict hygiene compliance. Low Maintenance: Built from high-durability materials, KDV’s glass-lined valves require minimal maintenance, helping industries reduce labor costs and improve operational efficiency How Glass-Lined Valves Are Built: 1.Core Material Selection: The base structure of the valve is typically made from a durable metal, such as cast steel, carbon steel, or stainless steel. This provides the valve with mechanical strength to handle pressure and stress. 2.Preparation of the Base Surface: The inner surfaces of the valve body are thoroughly cleaned and treated to ensure adhesion. This involves: Sandblasting or grinding to create a rough surface. Cleaning to remove any grease, dirt, or residue. 3.Glass Coating Application: Glass Composition: The glass lining is made from a specific blend of silica, borates, and other additives tailored to resist chemical corrosion and temperature fluctuations. Application Process: The glass is applied in powder or slurry form, coating the internal surfaces of the valve. This can be done manually or using automated equipment to ensure even application. 4.Firing Process: The coated valve is placed in a high-temperature kiln and fired at temperatures between 800°C and 1,000°C. During this process: The glass melts and forms a smooth, uniform layer. The glass bonds chemically and mechanically to the metal surface. 5.Quality Inspection and Finishing: The valve is inspected for defects like cracks, uneven coatings, or bubbles. Any imperfections are repaired through additional firing or re-coating. The valve is then assembled with components like seats, seals, and actuators.
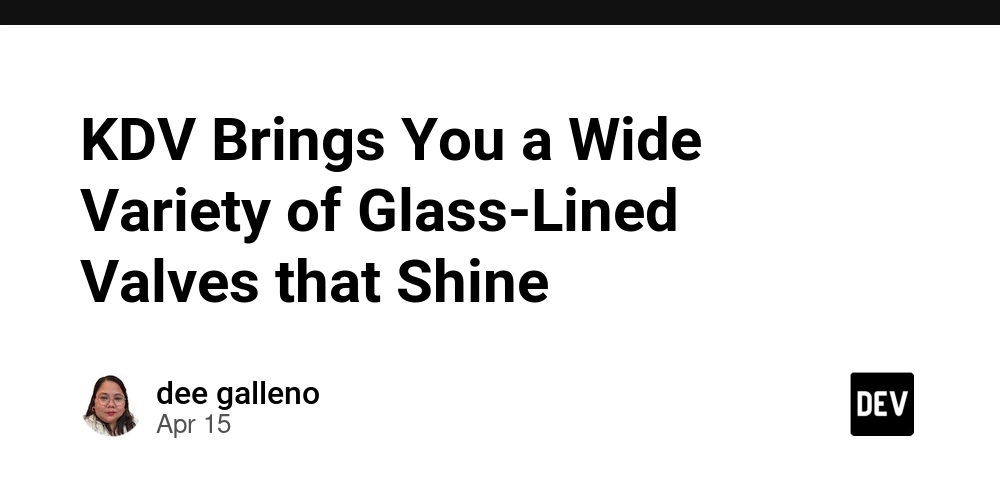
Corrosion, wear, and strict hygiene requirements can make industrial operations challenging. That’s where KDV’s glass-lined diaphragm valves come in. Engineered for durability and reliability, these valves are built to withstand aggressive chemicals, abrasive materials, and harsh environments while delivering exceptional performance.
Why KDV’s Glass-Lined Diaphragm Valves Outperform Other Types of Valve
Not all valves are built to withstand the harsh realities of industrial applications, where exposure to aggressive chemicals, extreme temperatures, and strict hygiene requirements can lead to rapid deterioration. That’s why KDV’s glass-lined valves are the preferred choice for industries demanding long-term performance, reliability, and efficiency.
MUST KNOW:
Glass is one of the most chemically resistant materials available, impervious to nearly all acids except hydrofluoric acid. This makes glass-lined valves the ultimate defense against corrosion in chemical processing and pharmaceutical industries, where even stainless steel can degrade over time.
Longer Lifespans: Glass-lined diaphragm valves significantly outlast traditional valve types in corrosive and abrasive environments, reducing downtime, maintenance costs, and process interruptions.
Versatile Across Industries – Our extensive range of glass-lined valves, including the weir-type diaphragm valve, is designed for applications requiring precision flow control, superior corrosion resistance, and strict hygiene compliance.
Low Maintenance: Built from high-durability materials, KDV’s glass-lined valves require minimal maintenance, helping industries reduce labor costs and improve operational efficiency
How Glass-Lined Valves Are Built:
1.Core Material Selection:
The base structure of the valve is typically made from a durable metal, such as cast steel, carbon steel, or stainless steel. This provides the valve with mechanical strength to handle pressure and stress.
2.Preparation of the Base Surface:
The inner surfaces of the valve body are thoroughly cleaned and treated to ensure adhesion. This involves:
Sandblasting or grinding to create a rough surface.
Cleaning to remove any grease, dirt, or residue.
3.Glass Coating Application:
Glass Composition: The glass lining is made from a specific blend of silica, borates, and other additives tailored to resist chemical corrosion and temperature fluctuations.
Application Process: The glass is applied in powder or slurry form, coating the internal surfaces of the valve. This can be done manually or using automated equipment to ensure even application.
4.Firing Process:
The coated valve is placed in a high-temperature kiln and fired at temperatures between 800°C and 1,000°C. During this process:
The glass melts and forms a smooth, uniform layer.
The glass bonds chemically and mechanically to the metal surface.
5.Quality Inspection and Finishing:
The valve is inspected for defects like cracks, uneven coatings, or bubbles.
Any imperfections are repaired through additional firing or re-coating.
The valve is then assembled with components like seats, seals, and actuators.