How Smart Factories Are Using AI to Revolutionize Production Scheduling and Cut Costs
Forget whiteboards and gut feelings. AI’s now the plant manager you wish you had — 24/7, tireless, and really into data. Introduction: The Need for Smarter Scheduling In the fast-paced world of manufacturing, traditional scheduling methods often fall short in addressing the complexities of modern production environments. Enter Artificial Intelligence (AI), poised to revolutionize production scheduling by offering dynamic, data-driven solutions that adapt in real-time. The High Cost of Inefficient Scheduling Traditional scheduling methods can lead to: Increased operational costs due to inefficiencies. Extended lead times are affecting delivery schedules. Underutilized resources, leading to wasted capacity. These inefficiencies can result in significant financial losses and decreased customer satisfaction. AI to the Rescue: Transforming Production Scheduling AI-driven production scheduling offers: Real-time adaptability to disruptions like supply chain delays or machine failures. Predictive analytics to forecast demand and potential disruptions. Optimized resource allocation, ensuring efficient use of machinery and labor. For instance, AI-based demand sensing in chemical manufacturing has enabled companies to adjust production schedules proactively, reducing waste and improving efficiency. Real-World Success Stories BMW's Virtual Factory BMW employs AI to create virtual simulations of its assembly lines, allowing for detailed planning and optimization. This strategy has led to enhanced efficiency and reduced risks associated with real-world experimentation. (wired.com) Priestley's Gourmet Delights A Queensland-based bakery, Priestley's Gourmet Delights, has opened a $53 million AI-powered smart factory, doubling production capacity and creating job opportunities. Sinopec's Smart Factories China Petrochemical Corporation, Sinopec, collaborated with Huawei to develop smart factories, resulting in a 10% increase in labor productivity. The Science Behind AI Scheduling Recent research highlights the effectiveness of AI in production scheduling: Deep Reinforcement Learning (DRL): DRL-based methods outperform traditional algorithms in generating near-optimal solutions for complex scheduling problems. Predictive Maintenance: AI analyzes sensor data to forecast equipment failures, enabling proactive maintenance and reducing downtime. Implementing AI in Your Factory Steps to integrate AI into production scheduling: Assess Current Systems: Evaluate existing processes to identify areas where AI can add value. Choose the Right Tools: Select AI solutions that align with your operational needs and can integrate with current systems. Train Your Team: Ensure staff are equipped with the necessary skills to work alongside AI technologies. Monitor and Adjust: Continuously analyze AI performance and make adjustments to optimize outcomes. Implementing AI requires careful planning, but the long-term benefits in efficiency and cost savings are substantial. | Factor | Traditional Scheduling | AI-Powered Scheduling | |----------------------|--------------------------------------------|---------------------------------------------------------| | Forecast Accuracy | 60–70% (static historical data) | 90–95% (real-time + historical + market trends) | | Adaptability | Manual re-planning | Real-time auto-adjustments | | Downtime Management | Reactive | Predictive (via IoT & ML alerts) | | Resource Utilization | Suboptimal, siloed planning | Optimized with plant-wide visibility | | Inventory Costs | Higher (stockouts or overproduction) | Reduced with precise demand forecasting | | Labor Planning | Rigid schedules | Dynamic based on production loads | | Energy Consumption | Higher | Lower (load balancing with AI) | | Decision-Making Speed| Slow (hours/days) | Instant (AI algorithms + dashboards) | | Scalability | Manual-heavy expansion | Easily scalable across sites | | Visibility & Insights| Low | High (centralized dashboards + analytics) | At AQe Digital, your digital transformation partner we empower manufacturing leaders to break free from outdated legacy systems and siloed planning. Our AI-driven smart factory solutions are crafted to boost throughput, reduce operational waste, and enable real-time decision-making on the shop floor. Whether you're running a mid-sized plant or managing multiple facilities, AQe Digital offers customized, scalab
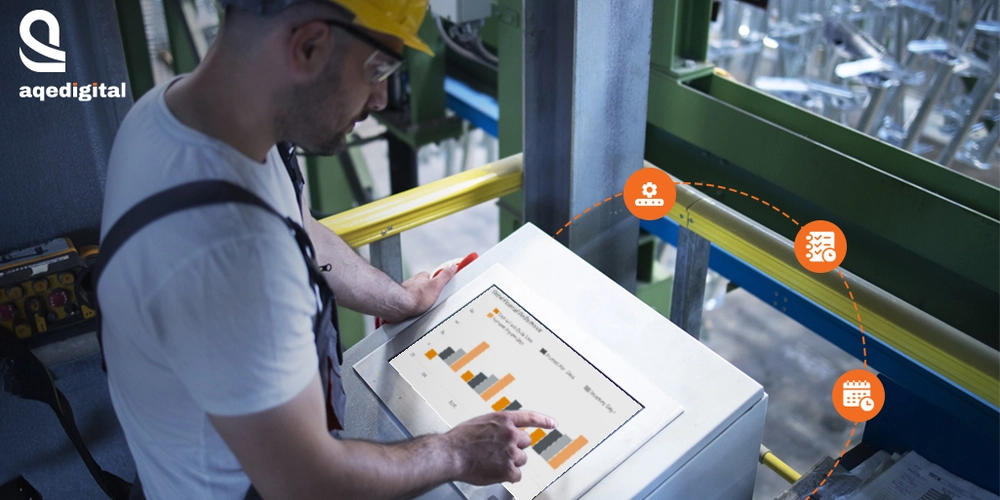
Forget whiteboards and gut feelings. AI’s now the plant manager you wish you had — 24/7, tireless, and really into data.
Introduction: The Need for Smarter Scheduling
In the fast-paced world of manufacturing, traditional scheduling methods often fall short in addressing the complexities of modern production environments. Enter Artificial Intelligence (AI), poised to revolutionize production scheduling by offering dynamic, data-driven solutions that adapt in real-time.
The High Cost of Inefficient Scheduling
Traditional scheduling methods can lead to:
- Increased operational costs due to inefficiencies.
- Extended lead times are affecting delivery schedules.
- Underutilized resources, leading to wasted capacity.
These inefficiencies can result in significant financial losses and decreased customer satisfaction.
AI to the Rescue: Transforming Production Scheduling
AI-driven production scheduling offers:
- Real-time adaptability to disruptions like supply chain delays or machine failures.
- Predictive analytics to forecast demand and potential disruptions.
- Optimized resource allocation, ensuring efficient use of machinery and labor.
For instance, AI-based demand sensing in chemical manufacturing has enabled companies to adjust production schedules proactively, reducing waste and improving efficiency.
Real-World Success Stories
- BMW's Virtual Factory
BMW employs AI to create virtual simulations of its assembly lines, allowing for detailed planning and optimization. This strategy has led to enhanced efficiency and reduced risks associated with real-world experimentation. (wired.com)
- Priestley's Gourmet Delights
A Queensland-based bakery, Priestley's Gourmet Delights, has opened a $53 million AI-powered smart factory, doubling production capacity and creating job opportunities.
China Petrochemical Corporation, Sinopec, collaborated with Huawei to develop smart factories, resulting in a 10% increase in labor productivity.
The Science Behind AI Scheduling
Recent research highlights the effectiveness of AI in production scheduling:
Deep Reinforcement Learning (DRL): DRL-based methods outperform traditional algorithms in generating near-optimal solutions for complex scheduling problems.
Predictive Maintenance: AI analyzes sensor data to forecast equipment failures, enabling proactive maintenance and reducing downtime.
Implementing AI in Your Factory
- Steps to integrate AI into production scheduling:
- Assess Current Systems: Evaluate existing processes to identify areas where AI can add value.
- Choose the Right Tools: Select AI solutions that align with your operational needs and can integrate with current systems.
- Train Your Team: Ensure staff are equipped with the necessary skills to work alongside AI technologies.
- Monitor and Adjust: Continuously analyze AI performance and make adjustments to optimize outcomes.
Implementing AI requires careful planning, but the long-term benefits in efficiency and cost savings are substantial.
| Factor | Traditional Scheduling | AI-Powered Scheduling |
|----------------------|--------------------------------------------|---------------------------------------------------------|
| Forecast Accuracy | 60–70% (static historical data) | 90–95% (real-time + historical + market trends) |
| Adaptability | Manual re-planning | Real-time auto-adjustments |
| Downtime Management | Reactive | Predictive (via IoT & ML alerts) |
| Resource Utilization | Suboptimal, siloed planning | Optimized with plant-wide visibility |
| Inventory Costs | Higher (stockouts or overproduction) | Reduced with precise demand forecasting |
| Labor Planning | Rigid schedules | Dynamic based on production loads |
| Energy Consumption | Higher | Lower (load balancing with AI) |
| Decision-Making Speed| Slow (hours/days) | Instant (AI algorithms + dashboards) |
| Scalability | Manual-heavy expansion | Easily scalable across sites |
| Visibility & Insights| Low | High (centralized dashboards + analytics) |
At AQe Digital, your digital transformation partner we empower manufacturing leaders to break free from outdated legacy systems and siloed planning. Our AI-driven smart factory solutions are crafted to boost throughput, reduce operational waste, and enable real-time decision-making on the shop floor.
Whether you're running a mid-sized plant or managing multiple facilities, AQe Digital offers customized, scalable production scheduling systems that seamlessly integrate with your ERP, MES, and IoT infrastructure — delivering measurable ROI from Day 1.