Grit Size Selection Guide for Abrasive Blasting: How to Avoid Common Mistakes?
In manufacturing, abrasive blasting is a critical surface treatment process, and the choice of media grit size directly impacts results, cost, and efficiency. However, engineers and procurement managers often fall into pitfalls due to insufficient understanding of grit characteristics. This article systematically explains grit selection logic and provides solutions to common issues, empowering optimized decision-making. I. Core Principles of Grit Selection The grit size (particle size) of blasting media must align with treatment goals, material properties, and equipment parameters. Key considerations include: 1. Surface Roughness Requirements Rough surfaces (e.g., pre-coating treatment): Use coarser grits (e.g., 20-40 mesh quartz sand or S70 steel grit) to create uniform texture for enhanced coating adhesion. Smooth surfaces (e.g., polishing or decorative finishes): Opt for finer grits (e.g., 170-325 mesh glass beads or baking soda) to achieve matte or satin effects with gentle impact. 2. Material Hardness and Workpiece Characteristics Hard materials (e.g., steel): Choose high-hardness, coarse grit media (e.g., aluminum oxide or steel grit) to avoid inefficiency from overly fine particles. Soft materials (e.g., aluminum or plastics): Use fine, low-density media (e.g., plastic pellets or walnut shells) to prevent surface damage. 3. Process Efficiency and Cost Coarse grit removes contaminants faster but wears quicker. Fine grit (e.g., reusable glass beads up to 30 cycles) suits long-term cost control. II. Common Mistakes and Solutions Mistake 1: Assuming Larger Grit Always Delivers Better Results Issue: Overusing coarse grit risks over-cutting or damaging precision parts. Solution: Match grit to specific tasks: For example, 40-60 mesh steel grit for rust removal vs. 80-120 mesh glass beads for delicate components. Adjust equipment pressure: Pair fine grit with high-pressure systems to enhance efficiency without excessive impact. Mistake 2: Ignoring Media Shape and Material Synergy Issue: Focusing solely on grit size while neglecting media type (e.g., round glass beads vs. angular aluminum oxide). Solution: Round media (e.g., glass beads): Ideal for polishing and deburring to create uniform finishes. Angular media (e.g., garnet): Optimized for aggressive cleaning or surface profiling. Mistake 3: Overlooking Environmental and Safety Constraints Issue: Using silica sand poses health risks (e.g., silicosis). Solution: Prioritize eco-friendly alternatives (e.g., glass beads, steel grit, or walnut shells) and install dust collection systems. III. Best Practices for Grit Selection 1. Stepwise Testing and Validation Pilot tests: Experiment with grit combinations (e.g., coarse + fine mixes) to balance speed and finish quality. Surface profiling: Use profilometers to measure roughness against standards like Sa2.5 cleanliness. 2. Industry Application References Automotive: 24-36 mesh steel grit for wheel hub descaling. Electronics: 120-200 mesh glass beads for micro-component polishing. 3. Dynamic Adjustments and Maintenance Sieve media regularly: Remove fractured particles to maintain grit consistency. Monitor equipment: Air pressure and nozzle wear affect grit performance. IV. Frequently Asked Questions (FAQ) Q1: What does a grit designation like "20 mesh" mean? A1: "Mesh" refers to the number of screen openings per square inch. Higher numbers indicate finer particles (e.g., 20 mesh ≈ 850 microns, 100 mesh ≈ 150 microns). Q2: How to evaluate if the current grit size is appropriate? A2: Inspect surface uniformity. Patchy abrasion or residual contaminants signal a need to adjust grit size or mixing ratios. Q3: Are there general grit size recommendations? A3: Typical applications include: Heavy rust removal: 20-40 mesh steel grit or aluminum oxide. Pre-coating preparation: 40-80 mesh quartz sand or garnet. Precision polishing: 120-325 mesh glass beads or plastic media. Selecting abrasive blasting grit requires balancing science and practical experience. By avoiding common errors and aligning grit with process needs, manufacturers can improve surface quality while reducing costs. Regularly engage with equipment suppliers and industry peers to stay updated on emerging technologies.
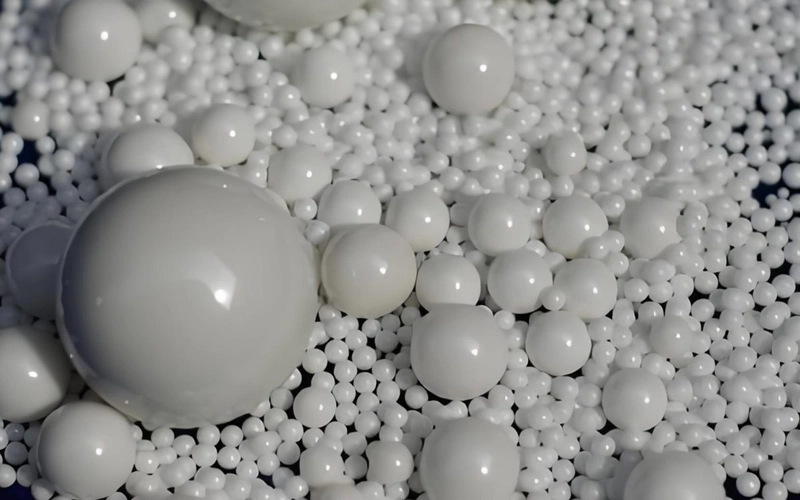
In manufacturing, abrasive blasting is a critical surface treatment process, and the choice of media grit size directly impacts results, cost, and efficiency. However, engineers and procurement managers often fall into pitfalls due to insufficient understanding of grit characteristics. This article systematically explains grit selection logic and provides solutions to common issues, empowering optimized decision-making.
I. Core Principles of Grit Selection
The grit size (particle size) of blasting media must align with treatment goals, material properties, and equipment parameters. Key considerations include:
1. Surface Roughness Requirements
Rough surfaces (e.g., pre-coating treatment): Use coarser grits (e.g., 20-40 mesh quartz sand or S70 steel grit) to create uniform texture for enhanced coating adhesion.
Smooth surfaces (e.g., polishing or decorative finishes): Opt for finer grits (e.g., 170-325 mesh glass beads or baking soda) to achieve matte or satin effects with gentle impact.
2. Material Hardness and Workpiece Characteristics
Hard materials (e.g., steel): Choose high-hardness, coarse grit media (e.g., aluminum oxide or steel grit) to avoid inefficiency from overly fine particles.
Soft materials (e.g., aluminum or plastics): Use fine, low-density media (e.g., plastic pellets or walnut shells) to prevent surface damage.
3. Process Efficiency and Cost
Coarse grit removes contaminants faster but wears quicker. Fine grit (e.g., reusable glass beads up to 30 cycles) suits long-term cost control.
II. Common Mistakes and Solutions
Mistake 1: Assuming Larger Grit Always Delivers Better Results
Issue: Overusing coarse grit risks over-cutting or damaging precision parts.
Solution:
Match grit to specific tasks: For example, 40-60 mesh steel grit for rust removal vs. 80-120 mesh glass beads for delicate components.
Adjust equipment pressure: Pair fine grit with high-pressure systems to enhance efficiency without excessive impact.
Mistake 2: Ignoring Media Shape and Material Synergy
Issue: Focusing solely on grit size while neglecting media type (e.g., round glass beads vs. angular aluminum oxide).
Solution:
Round media (e.g., glass beads): Ideal for polishing and deburring to create uniform finishes.
Angular media (e.g., garnet): Optimized for aggressive cleaning or surface profiling.
Mistake 3: Overlooking Environmental and Safety Constraints
Issue: Using silica sand poses health risks (e.g., silicosis).
Solution:
Prioritize eco-friendly alternatives (e.g., glass beads, steel grit, or walnut shells) and install dust collection systems.
III. Best Practices for Grit Selection
1. Stepwise Testing and Validation
Pilot tests: Experiment with grit combinations (e.g., coarse + fine mixes) to balance speed and finish quality.
Surface profiling: Use profilometers to measure roughness against standards like Sa2.5 cleanliness.
2. Industry Application References
Automotive: 24-36 mesh steel grit for wheel hub descaling.
Electronics: 120-200 mesh glass beads for micro-component polishing.
3. Dynamic Adjustments and Maintenance
Sieve media regularly: Remove fractured particles to maintain grit consistency.
Monitor equipment: Air pressure and nozzle wear affect grit performance.
IV. Frequently Asked Questions (FAQ)
Q1: What does a grit designation like "20 mesh" mean?
A1: "Mesh" refers to the number of screen openings per square inch. Higher numbers indicate finer particles (e.g., 20 mesh ≈ 850 microns, 100 mesh ≈ 150 microns).
Q2: How to evaluate if the current grit size is appropriate?
A2: Inspect surface uniformity. Patchy abrasion or residual contaminants signal a need to adjust grit size or mixing ratios.
Q3: Are there general grit size recommendations?
A3: Typical applications include:
Heavy rust removal: 20-40 mesh steel grit or aluminum oxide.
Pre-coating preparation: 40-80 mesh quartz sand or garnet.
Precision polishing: 120-325 mesh glass beads or plastic media.
Selecting abrasive blasting grit requires balancing science and practical experience. By avoiding common errors and aligning grit with process needs, manufacturers can improve surface quality while reducing costs. Regularly engage with equipment suppliers and industry peers to stay updated on emerging technologies.