6 Ways Data Analytics Powers Smarter Manufacturing
Data is redefining manufacturing. As Industry 4.0 evolves, factories are becoming smarter, more connected, and more agile—thanks to data analytics. Below are six major ways analytics is helping manufacturers get ahead: 1. Predictive Maintenance with Data Models Using historical sensor data, ML models can predict when a machine is likely to fail. This allows for maintenance to be scheduled before downtime happens—saving money and improving production rates. 2. Defect Detection and Root Cause Analysis With real-time monitoring, manufacturers can flag quality issues during production. Algorithms can help trace problems back to specific processes or components for faster resolution. 3. Performance Benchmarking Across Facilities Analytics enables comparisons between production lines, shifts, or entire plants. This empowers teams to spot inefficiencies and replicate best practices across the organization. 4. Supply Chain Predictive Analytics By analyzing trends in supplier performance, demand fluctuations, and shipping data, manufacturers can proactively manage inventory and avoid stockouts or overstocking. 5. IoT-Enabled Operational Dashboards Smart factories equipped with IoT sensors feed data into centralized dashboards. Operators and engineers get real-time visibility into metrics like throughput, equipment performance, and safety alerts. 6. Data-Driven Strategy Long-term planning is vastly improved when backed by accurate data. Whether it’s expanding to new markets, optimizing capacity, or launching new lines, strategic insights come from real numbers—not guesswork. Why It Matters Data analytics isn't just a backend reporting function—it’s core to lean operations, faster delivery, and smarter decisions in manufacturing. Read the original article here:
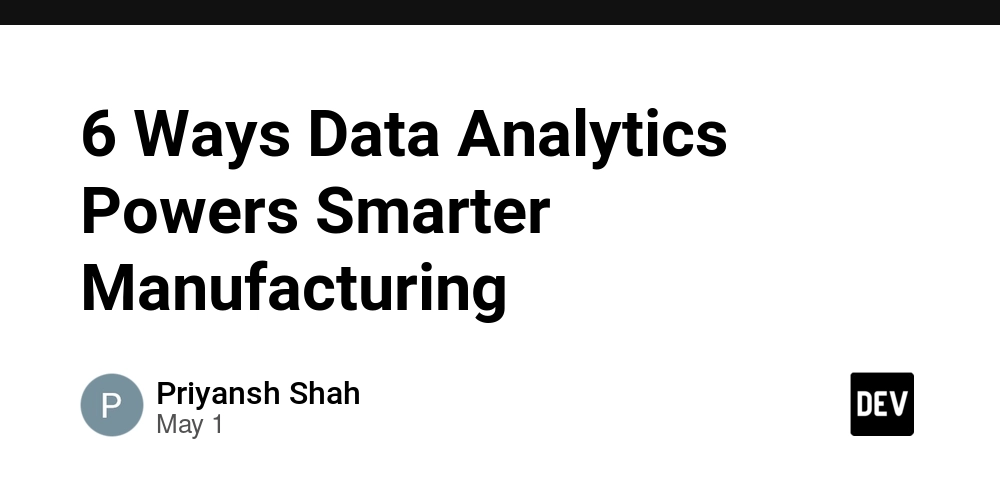
Data is redefining manufacturing. As Industry 4.0 evolves, factories are becoming smarter, more connected, and more agile—thanks to data analytics.
Below are six major ways analytics is helping manufacturers get ahead:
1. Predictive Maintenance with Data Models
Using historical sensor data, ML models can predict when a machine is likely to fail. This allows for maintenance to be scheduled before downtime happens—saving money and improving production rates.
2. Defect Detection and Root Cause Analysis
With real-time monitoring, manufacturers can flag quality issues during production. Algorithms can help trace problems back to specific processes or components for faster resolution.
3. Performance Benchmarking Across Facilities
Analytics enables comparisons between production lines, shifts, or entire plants. This empowers teams to spot inefficiencies and replicate best practices across the organization.
4. Supply Chain Predictive Analytics
By analyzing trends in supplier performance, demand fluctuations, and shipping data, manufacturers can proactively manage inventory and avoid stockouts or overstocking.
5. IoT-Enabled Operational Dashboards
Smart factories equipped with IoT sensors feed data into centralized dashboards. Operators and engineers get real-time visibility into metrics like throughput, equipment performance, and safety alerts.
6. Data-Driven Strategy
Long-term planning is vastly improved when backed by accurate data. Whether it’s expanding to new markets, optimizing capacity, or launching new lines, strategic insights come from real numbers—not guesswork.
Why It Matters
Data analytics isn't just a backend reporting function—it’s core to lean operations, faster delivery, and smarter decisions in manufacturing.