Green and Eco-Friendly Blasting Media: Current Development, Trends, and Future Challenges
——An In-Depth Industry Analysis for Manufacturing Managers and Environmental Engineers Introduction: The Revolution of Blasting Technology in the Era of Environmental Transformation As global environmental regulations tighten (e.g., EU REACH, U.S. EPA standards) and the ESG (Environmental, Social, Governance) concept gains traction, the manufacturing industry is increasingly demanding sustainable surface treatment technologies. Traditional blasting media, such as silica sand and steel grit, are under scrutiny due to dust pollution, high energy consumption, and health risks. In contrast, green and eco-friendly blasting media are emerging as a core breakthrough for industry transformation. This article combines the latest market data and technological trends to analyze the current development and future challenges in this field, providing strategic insights for decision-makers. I. Market Status: Policy-Driven Growth and Technological Advancements 1. Market Size and Growth Potential According to Grand View Research, the global blasting media market reached $5.2 billion in 2023, with the share of eco-friendly media rising from 12% in 2018 to 28% in 2023, achieving a compound annual growth rate (CAGR) of 9.7%. By 2030, the market share of green media is expected to exceed 45%, with the Asia-Pacific region (especially China and India) becoming a growth engine due to manufacturing upgrade demands. 2. Mainstream Eco-Friendly Media Types Plant-Based Materials (walnut shells, corn cobs): Biodegradable, low dust emission (70% less than silica sand), suitable for precision parts. Synthetic Ceramic Particles (alumina, silicon carbide): High hardness, reusable 5-8 times, reducing long-term costs. Ice/Dry Ice: Zero-residue technology, with over 40% penetration in the aerospace sector. Recycled Glass Beads: Made from waste glass, reducing carbon emissions by 65% compared to traditional processes. 3. Policy and Industry Standards Driving Adoption The EU Circular Economy Action Plan aims to increase industrial waste recycling to 70% by 2030. China’s 14th Five-Year Plan tightens blasting dust emission limits to 10mg/m³ (previously 20mg/m³). Automotive giants (e.g., Toyota, Volkswagen) have incorporated "green blasting certification" into supply chain standards. II. Technological Advantages and Business Value: Why Choose Green Media? 1. Environmental Benefits Dust Control: Plant-based media reduce dust concentration to
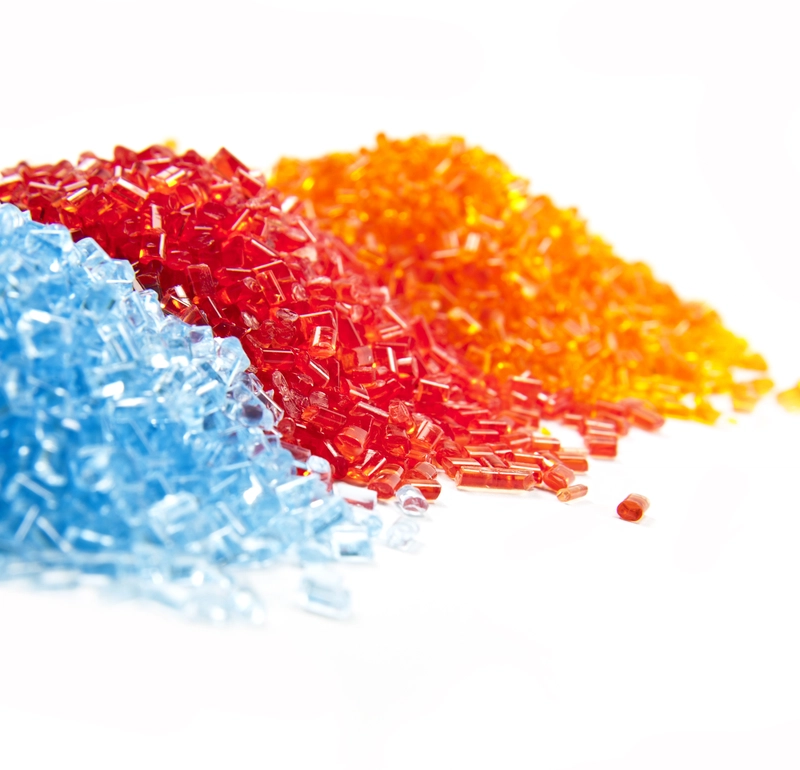
——An In-Depth Industry Analysis for Manufacturing Managers and Environmental Engineers
Introduction: The Revolution of Blasting Technology in the Era of Environmental Transformation
As global environmental regulations tighten (e.g., EU REACH, U.S. EPA standards) and the ESG (Environmental, Social, Governance) concept gains traction, the manufacturing industry is increasingly demanding sustainable surface treatment technologies. Traditional blasting media, such as silica sand and steel grit, are under scrutiny due to dust pollution, high energy consumption, and health risks. In contrast, green and eco-friendly blasting media are emerging as a core breakthrough for industry transformation. This article combines the latest market data and technological trends to analyze the current development and future challenges in this field, providing strategic insights for decision-makers.
I. Market Status: Policy-Driven Growth and Technological Advancements
1. Market Size and Growth Potential
According to Grand View Research, the global blasting media market reached $5.2 billion in 2023, with the share of eco-friendly media rising from 12% in 2018 to 28% in 2023, achieving a compound annual growth rate (CAGR) of 9.7%. By 2030, the market share of green media is expected to exceed 45%, with the Asia-Pacific region (especially China and India) becoming a growth engine due to manufacturing upgrade demands.
2. Mainstream Eco-Friendly Media Types
- Plant-Based Materials (walnut shells, corn cobs): Biodegradable, low dust emission (70% less than silica sand), suitable for precision parts.
- Synthetic Ceramic Particles (alumina, silicon carbide): High hardness, reusable 5-8 times, reducing long-term costs.
- Ice/Dry Ice: Zero-residue technology, with over 40% penetration in the aerospace sector.
- Recycled Glass Beads: Made from waste glass, reducing carbon emissions by 65% compared to traditional processes.
3. Policy and Industry Standards Driving Adoption
The EU Circular Economy Action Plan aims to increase industrial waste recycling to 70% by 2030.
China’s 14th Five-Year Plan tightens blasting dust emission limits to 10mg/m³ (previously 20mg/m³).
Automotive giants (e.g., Toyota, Volkswagen) have incorporated "green blasting certification" into supply chain standards.
II. Technological Advantages and Business Value: Why Choose Green Media?
1. Environmental Benefits
- Dust Control: Plant-based media reduce dust concentration to <2mg/m³ (compared to 15-20mg/m³ for silica sand), lowering the risk of silicosis.
- Carbon Reduction: Each ton of recycled glass beads reduces CO₂ emissions by 1.2 tons compared to new steel grit.
- Waste Management: 95% of synthetic ceramic media can be recycled, reducing landfill costs.
2. Economic Breakthroughs
- Lower Lifecycle Costs: In the automotive industry, switching to ice media reduced annual maintenance costs by 18% per production line (source: Frost & Sullivan).
- Improved Efficiency: High-precision ceramic particles increase blasting speed by 30% and reduce rework rates.
III. Future Challenges: Technological Bottlenecks and Industry Collaboration
1. Technical Pain Points
- Material Limitations: Plant-based media have low hardness (Mohs 2-3), making them unsuitable for hard substrates like high-strength steel.
- Cost Barriers: Green media prices remain 20-50% higher than traditional materials, hindering adoption by SMEs.
- Lack of Recycling Systems: Only 35% of global companies have media recycling equipment, relying on third-party processing.
2. Industry Collaboration Challenges
- Lack of Standardization: Differing definitions of "eco-friendly media" across countries create barriers to cross-border procurement.
- Insufficient R&D Investment: SMEs lack funding for new material testing (single certification costs exceed $50,000).
IV. Solutions: Innovation and Ecosystem Building
1. Technological Breakthrough Paths
- Composite Material Development: For example, "bio-resin + ceramic" hybrid media balancing hardness and biodegradability.
- Smart Blasting Equipment: AI algorithms optimize media usage, reducing waste.
- Cryogenic Plasma Technology: A zero-media alternative to physical blasting (currently in the lab stage).
2. Industry Ecosystem Recommendations
- Policy Subsidies: Governments should offer tax credits for green media procurement (e.g., U.S. IRA Act).
- Industry Alliances: Establish cross-company recycling networks to share regeneration facilities.
- Customer Education: Use Life Cycle Assessment (LCA) reports to quantify long-term benefits and boost decision-maker confidence.
V. Conclusion: Green Blasting—A Must for Sustainable Manufacturing
Eco-friendly blasting media are not just a compliance requirement but a strategic choice for cost reduction, efficiency improvement, and brand value enhancement. To overcome the dual challenges of technological evolution and market education, innovation, policy coordination, and industry collaboration are essential to transition this field from an "optional solution" to an "industry standard."
Keywords: Green blasting media, eco-friendly surface treatment, sustainable manufacturing, blasting technology trends, industrial carbon neutrality, ESG compliance
Data Sources: Grand View Research, Frost & Sullivan, European Environment Agency, China Ministry of Ecology and Environment.
Further Reading:
- 2024 Global Surface Treatment Technology White Paper
- Pathways to Carbon Neutrality in Manufacturing: Starting with Blasting Processes