How to focus on “Made in America”
If you were to establish an electric truck company today, would the trucks be built in America? In April 2025, the answer is yes. In 2022, even after the pandemic, the answer might have been different. That was the year I initially founded Chang Robotics, a company that manufactures what we believe to be one of the world’s most powerful battery-operated commercial rigs. Its first commercial use will be for fast snow removal in airports and other mission-critical facilities. At the time, advisors, investors, and partners all said “Let’s take this to China. I’ll bet we could get this done in six months.” I declined. New Manufacturing Should Focus on Being American Made For companies already in production, of course, the answer may be different. Even if the current tariffs remain in place, immediate shifts can be prohibitively expensive and difficult. I’ll talk more about that in a future column. In my own case, only one person agreed with me—Marc Manning, a remarkable mechanical engineer and vehicle architect with extensive experience in helping organizations transition to cleaner technologies. Marc is now CEO of Kodiak Technologies, a company I founded, precisely because of his ability to meet a challenge like this when others couldn’t. I tell you this for two reasons: To reinforce how emphatically I believe manufacturing in America will strengthen U.S. companies and its economy and workforce. To compel every entrepreneur to think differently—even wildly differently—as you innovate the products you build. Here’s an example. We designed and built our hybrid electric machine to be used for snow removal in airports. We chose this niche product because airports must keep their runways snow-free at all times. For airports close to the snow line, the massive equipment required to meet these requirements may only be used a few days of the year. So, we designed our machine with a dual power capability that allows the equipment to serve as a micro-grid power source when the equipment is not removing snow. Airports can use this equipment as back-up power, allowing for energy cost-shaving that reduces power costs. Our product allows airports to meet massive regulatory and safety requirement while also gaining power safety and savings, which encourages them buy an expensive piece of machinery. Other high-requirement facilities such as hospitals and municipal buildings could potentially benefit from our equipment as well. “Made in America” Protects your Supply Chain We strive to use this level of creativity in every product we create, and we urge and mentor other creators to adopt this level of thinking. As for our Made in America focus, for the past several years, and especially since the pandemic, there’s been a trend toward supply chain “near shoring”—confining any out-of-country production to the contiguous countries of Mexico, the United States, and Canada, as opposed to relying on materials from China and the European countries, to solidify and protect our supply chain from disruption. That movement has unveiled some surprising discoveries. When we delve into the creation of nearly every consumable good and product, we uncover a deeper reliance on foreign partners than we’d ever imagined. For example, the core materials in pharmaceuticals, aluminum, and steel products, even when obtained in America, are being shipped to Europe, China, or other locations for further refinement before being shipped back to America to complete our U.S. manufacturing goods. Knowing this, we and many others have been progressively moving much closer to North American and U.S. sourcing. In 2025, the shifts in tariff policies are further deepening these complexities. While I’d love to say we knew it all along, none of us is immune to the sudden changes in pricing and availability. Our own company was impacted the week I wrote this when the robots we ordered from Canada suddenly cost $100,000 more to obtain, due to robotic equipment having been coded as “light trucks,” seemingly to enjoy a lower tariff price at the border. At 2.5% tariff, the cost of this customs coding is small, but when higher tariffs kick in at 25%, the consequence is immense. My words of wisdom on this, for a supplier or provider, is to construct your contracts carefully to protect yourself from price changes or geopolitical events you could not have predicted. Beyond this, however, we need to increasingly strive to minimize transport distances and costs, to assure quality and safety, and to grow and protect American jobs. To this end, we advise all entrepreneurs to join us in becoming as close as possible to being a truly Made in America organization. Our future generations will thank us. Matthew Chang is the founder and CEO of Chang Robotics.
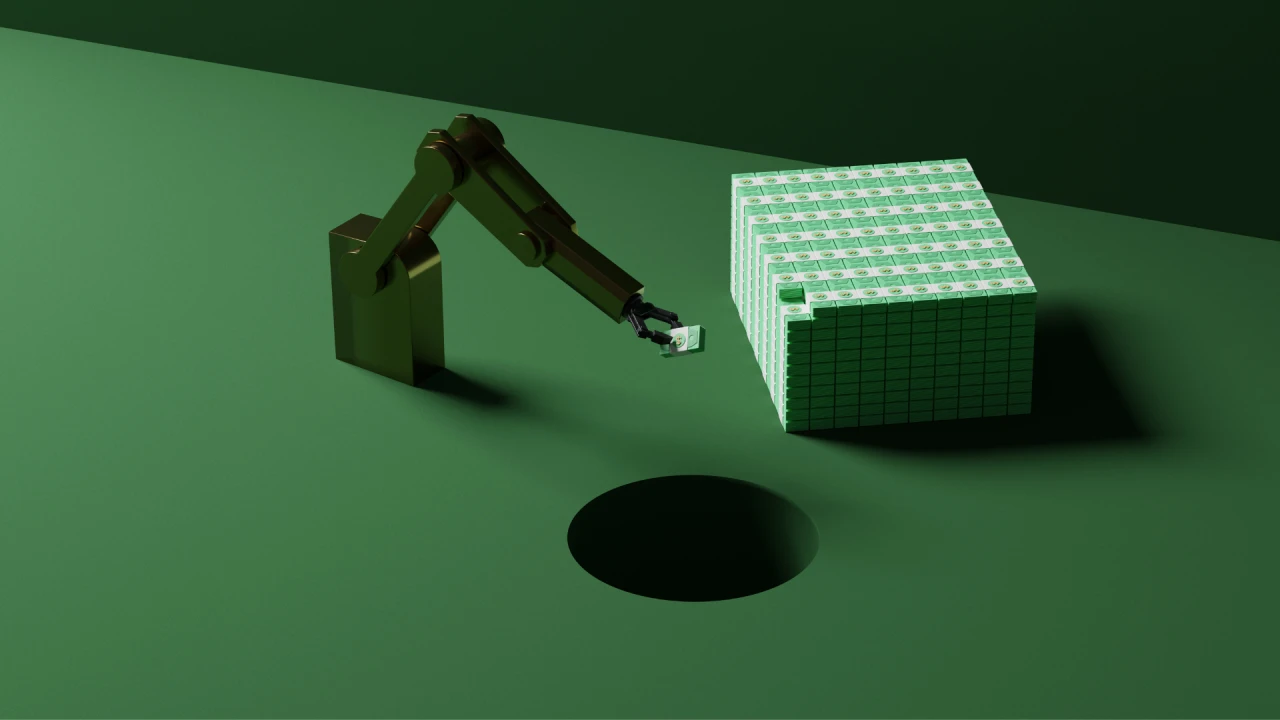
If you were to establish an electric truck company today, would the trucks be built in America? In April 2025, the answer is yes.
In 2022, even after the pandemic, the answer might have been different. That was the year I initially founded Chang Robotics, a company that manufactures what we believe to be one of the world’s most powerful battery-operated commercial rigs. Its first commercial use will be for fast snow removal in airports and other mission-critical facilities.
At the time, advisors, investors, and partners all said “Let’s take this to China. I’ll bet we could get this done in six months.”
I declined.
New Manufacturing Should Focus on Being American Made
For companies already in production, of course, the answer may be different. Even if the current tariffs remain in place, immediate shifts can be prohibitively expensive and difficult. I’ll talk more about that in a future column.
In my own case, only one person agreed with me—Marc Manning, a remarkable mechanical engineer and vehicle architect with extensive experience in helping organizations transition to cleaner technologies. Marc is now CEO of Kodiak Technologies, a company I founded, precisely because of his ability to meet a challenge like this when others couldn’t.
I tell you this for two reasons:
- To reinforce how emphatically I believe manufacturing in America will strengthen U.S. companies and its economy and workforce.
- To compel every entrepreneur to think differently—even wildly differently—as you innovate the products you build.
Here’s an example. We designed and built our hybrid electric machine to be used for snow removal in airports. We chose this niche product because airports must keep their runways snow-free at all times.
For airports close to the snow line, the massive equipment required to meet these requirements may only be used a few days of the year. So, we designed our machine with a dual power capability that allows the equipment to serve as a micro-grid power source when the equipment is not removing snow. Airports can use this equipment as back-up power, allowing for energy cost-shaving that reduces power costs. Our product allows airports to meet massive regulatory and safety requirement while also gaining power safety and savings, which encourages them buy an expensive piece of machinery. Other high-requirement facilities such as hospitals and municipal buildings could potentially benefit from our equipment as well.
“Made in America” Protects your Supply Chain
We strive to use this level of creativity in every product we create, and we urge and mentor other creators to adopt this level of thinking. As for our Made in America focus, for the past several years, and especially since the pandemic, there’s been a trend toward supply chain “near shoring”—confining any out-of-country production to the contiguous countries of Mexico, the United States, and Canada, as opposed to relying on materials from China and the European countries, to solidify and protect our supply chain from disruption.
That movement has unveiled some surprising discoveries. When we delve into the creation of nearly every consumable good and product, we uncover a deeper reliance on foreign partners than we’d ever imagined. For example, the core materials in pharmaceuticals, aluminum, and steel products, even when obtained in America, are being shipped to Europe, China, or other locations for further refinement before being shipped back to America to complete our U.S. manufacturing goods.
Knowing this, we and many others have been progressively moving much closer to North American and U.S. sourcing. In 2025, the shifts in tariff policies are further deepening these complexities.
While I’d love to say we knew it all along, none of us is immune to the sudden changes in pricing and availability. Our own company was impacted the week I wrote this when the robots we ordered from Canada suddenly cost $100,000 more to obtain, due to robotic equipment having been coded as “light trucks,” seemingly to enjoy a lower tariff price at the border. At 2.5% tariff, the cost of this customs coding is small, but when higher tariffs kick in at 25%, the consequence is immense.
My words of wisdom on this, for a supplier or provider, is to construct your contracts carefully to protect yourself from price changes or geopolitical events you could not have predicted. Beyond this, however, we need to increasingly strive to minimize transport distances and costs, to assure quality and safety, and to grow and protect American jobs. To this end, we advise all entrepreneurs to join us in becoming as close as possible to being a truly Made in America organization. Our future generations will thank us.
Matthew Chang is the founder and CEO of Chang Robotics.