How Supply Chain Delays Can Lead to Downtime in Manufacturing
In today’s fast-paced production environments, supply chain efficiency is just as important as machine performance. One weak link—whether it's a late shipment of raw materials or a miscommunication with suppliers—can ripple through the production line and result in downtime in manufacturing, costing companies thousands per hour in lost productivity. The Hidden Impact of Supply Chain Disruptions Supply chain issues often begin far from the factory floor, yet their consequences are felt most acutely at the production line. When critical materials or components don’t arrive on time, manufacturers are left with no choice but to halt operations. Even short-term supply gaps can derail production schedules, delay customer deliveries, and affect profitability. Beyond material shortages, disruptions also occur due to customs delays, transportation bottlenecks, or unpredictable geopolitical events. Without proper visibility and proactive planning, manufacturers risk significant downtime and reputational damage. Key Supply Chain Risks That Affect Production 1. Raw Material Shortages Global sourcing has become the norm, but reliance on international suppliers means even minor disruptions—like a port delay or factory shutdown overseas—can lead to major local consequences. Companies often lack visibility into second-tier suppliers, making it hard to predict when or where shortages will strike. Solution: Diversifying supplier networks and maintaining safety stock of critical materials helps mitigate the risk of shortages and maintain steady production flow. 2. Poor Supplier Communication Without real-time updates from suppliers, manufacturers operate with outdated or incomplete information. If a shipment is delayed and the production team doesn't know until the last minute, the result is wasted labor, idle machines, and a scramble to adjust. Solution: Implementing supplier portals and integrated communication systems allows real-time data exchange and proactive collaboration. Suppliers can update status changes instantly, giving manufacturers time to adapt. 3. Logistics and Transportation Delays From driver shortages to inclement weather, logistics issues can delay crucial deliveries. With many plants operating on just-in-time (JIT) inventory models, any delay—even by a few hours—can cause cascading disruptions. Solution: Collaborating with logistics partners for predictive ETA tracking, and using AI-based route optimization tools, helps reduce the impact of transportation-related downtime. Using Technology to Predict and Prevent Disruptions Manufacturers are increasingly turning to supply chain visibility platforms to reduce uncertainty. These systems collect data from across the entire supply network—from raw material origin points to warehouse inventory—offering a unified view in real time. By leveraging machine learning and predictive analytics, companies can forecast potential supply disruptions based on trends like vendor lead time variability or port congestion data. This insight empowers production teams to plan proactively, avoid unexpected material shortages, and maintain continuity. Building Resilient Supply Chains 1. Localize Where Possible Shifting to nearshore or onshore suppliers where practical reduces dependence on long transit times and international logistics. While not always feasible, even partial local sourcing can help mitigate global risk. 2. Develop Contingency Plans A resilient supply chain includes Plan B (and Plan C). Identify alternate suppliers, pre-vetted logistics partners, and emergency stockpiles for mission-critical components. Testing these scenarios regularly ensures readiness when disruption strikes. 3. Enhance Forecasting and Demand Planning Erratic ordering and last-minute changes create chaos across the supply chain. By improving demand forecasting through AI-driven models and historical data analysis, manufacturers can align material procurement more precisely with production needs. Collaboration Between Procurement and Production Too often, procurement and production teams operate in silos. Procurement may negotiate great deals or delay orders to save costs—but without input from production teams, this can result in material shortages at critical moments. Cross-functional collaboration is essential. Joint planning sessions, shared dashboards, and unified KPIs help align purchasing strategies with real-time production needs, reducing the risk of costly misalignments. Metrics to Monitor Supply Chain Health Tracking key supply chain metrics helps manufacturers identify risks early and improve performance: Supplier On-Time Delivery Rate Average Lead Time for Critical Materials Inventory Turnover Ratio Perfect Order Rate Supplier Risk Score Monitoring these KPIs helps spot weaknesses before they affect operations and supports better de
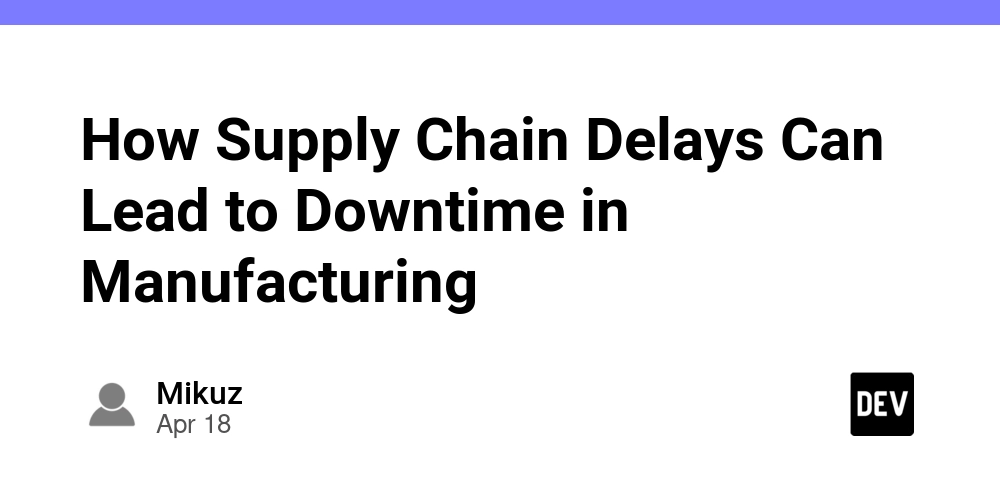
In today’s fast-paced production environments, supply chain efficiency is just as important as machine performance. One weak link—whether it's a late shipment of raw materials or a miscommunication with suppliers—can ripple through the production line and result in downtime in manufacturing, costing companies thousands per hour in lost productivity.
The Hidden Impact of Supply Chain Disruptions
Supply chain issues often begin far from the factory floor, yet their consequences are felt most acutely at the production line. When critical materials or components don’t arrive on time, manufacturers are left with no choice but to halt operations. Even short-term supply gaps can derail production schedules, delay customer deliveries, and affect profitability.
Beyond material shortages, disruptions also occur due to customs delays, transportation bottlenecks, or unpredictable geopolitical events. Without proper visibility and proactive planning, manufacturers risk significant downtime and reputational damage.
Key Supply Chain Risks That Affect Production
1. Raw Material Shortages
Global sourcing has become the norm, but reliance on international suppliers means even minor disruptions—like a port delay or factory shutdown overseas—can lead to major local consequences. Companies often lack visibility into second-tier suppliers, making it hard to predict when or where shortages will strike.
Solution: Diversifying supplier networks and maintaining safety stock of critical materials helps mitigate the risk of shortages and maintain steady production flow.
2. Poor Supplier Communication
Without real-time updates from suppliers, manufacturers operate with outdated or incomplete information. If a shipment is delayed and the production team doesn't know until the last minute, the result is wasted labor, idle machines, and a scramble to adjust.
Solution: Implementing supplier portals and integrated communication systems allows real-time data exchange and proactive collaboration. Suppliers can update status changes instantly, giving manufacturers time to adapt.
3. Logistics and Transportation Delays
From driver shortages to inclement weather, logistics issues can delay crucial deliveries. With many plants operating on just-in-time (JIT) inventory models, any delay—even by a few hours—can cause cascading disruptions.
Solution: Collaborating with logistics partners for predictive ETA tracking, and using AI-based route optimization tools, helps reduce the impact of transportation-related downtime.
Using Technology to Predict and Prevent Disruptions
Manufacturers are increasingly turning to supply chain visibility platforms to reduce uncertainty. These systems collect data from across the entire supply network—from raw material origin points to warehouse inventory—offering a unified view in real time.
By leveraging machine learning and predictive analytics, companies can forecast potential supply disruptions based on trends like vendor lead time variability or port congestion data. This insight empowers production teams to plan proactively, avoid unexpected material shortages, and maintain continuity.
Building Resilient Supply Chains
1. Localize Where Possible
Shifting to nearshore or onshore suppliers where practical reduces dependence on long transit times and international logistics. While not always feasible, even partial local sourcing can help mitigate global risk.
2. Develop Contingency Plans
A resilient supply chain includes Plan B (and Plan C). Identify alternate suppliers, pre-vetted logistics partners, and emergency stockpiles for mission-critical components. Testing these scenarios regularly ensures readiness when disruption strikes.
3. Enhance Forecasting and Demand Planning
Erratic ordering and last-minute changes create chaos across the supply chain. By improving demand forecasting through AI-driven models and historical data analysis, manufacturers can align material procurement more precisely with production needs.
Collaboration Between Procurement and Production
Too often, procurement and production teams operate in silos. Procurement may negotiate great deals or delay orders to save costs—but without input from production teams, this can result in material shortages at critical moments.
Cross-functional collaboration is essential. Joint planning sessions, shared dashboards, and unified KPIs help align purchasing strategies with real-time production needs, reducing the risk of costly misalignments.
Metrics to Monitor Supply Chain Health
Tracking key supply chain metrics helps manufacturers identify risks early and improve performance:
- Supplier On-Time Delivery Rate
- Average Lead Time for Critical Materials
- Inventory Turnover Ratio
- Perfect Order Rate
- Supplier Risk Score
Monitoring these KPIs helps spot weaknesses before they affect operations and supports better decision-making around sourcing and logistics.
Conclusion: Strong Supply Chains Keep Lines Running
While manufacturing teams work hard to keep machines running smoothly, they can’t perform if the parts they need aren’t available. Strengthening the supply chain is a direct investment in operational uptime. Companies that embrace real-time supply chain analytics, diversify their sources, and enhance cross-functional communication significantly reduce the chance of unexpected stoppages.
By prioritizing supply chain resilience, manufacturers safeguard their productivity, profitability, and reputation in an increasingly unpredictable global market.