Ceramic Sandblasting Beads vs. Plastic Sandblasting Beads
As one of the core processes in the field of surface treatment, sandblasting technology is crucial for material removal efficiency, surface roughness control, and cost optimization. The choice of sandblasting media, especially the comparison between ceramic sandblasting beads and plastic sandblasting beads, has become a key issue in engineers' decision-making. Based on technical parameters, application scenarios, and long-term benefits, this article will analyze the core differences between the two and provide scientific suggestions for selection. I. Comparative Analysis of Core Performance: Technical Parameters and Process Adaptability 1.Hardness and Wear Resistance Ceramic Sandblasting Beads (based on Al₂O₃/ZrO₂): With a hardness as high as Mohs 8-9, they can be reused more than 500-1000 times, showing significant long-term cost benefits. Plastic Sandblasting Beads (based on PA/PU): With a hardness of Mohs 2-3, the average lifespan is only 10-50 times. Frequent replacements lead to an increase in implicit costs. Applicable Scenarios: Ceramic beads are more suitable for high-intensity continuous operations (such as removing oxidation scale from automotive parts), while plastic beads are suitable for mild surface cleaning of precision electronic components or soft metals (such as aluminum and magnesium alloys) due to their low impact force. 2.Surface Treatment Effects Roughness Control: By adjusting the particle size (80-300 mesh), ceramic beads can achieve precise control of Ra 0.5-5μm, with a uniformity error of less than 5%; due to the easy deformation of plastic beads, the roughness fluctuation can reach 20%. Pollution Risk: Plastic beads may melt and adhere to the substrate under high-speed impact (especially in working conditions above 80℃), requiring additional cleaning procedures; ceramic beads have strong chemical inertness and no residue risk. 3.Environmental Protection and Compliance Microplastic Problem: Microplastic particles are generated after the wear of plastic sandblasting beads, facing regulatory restrictions of the EU's REACH and the US EPA, increasing the treatment cost by 30%-50%. Circular Economy: Ceramic sandblasting beads support 100% recycling and regeneration, meeting the requirements of ISO 14001 certification, and reducing the carbon footprint by more than 60%. II. Cost Model: Short-term Investment vs. Long-term Returns Cost Items Ceramic Sandblasting Beads PlasticSandblasting Beads Initial Unit Price $15-30/kg $5-10/kg Service Life 500-1000 times 10-50 times Annual Consumable Cost* $300-600 $2000-5000 Waste Disposal Cost $0 (recyclable) $50-100/ton *Assuming an annual consumption of 100kg and the equipment operates 300 days a year Conclusion: Ceramic sandblasting beads can achieve cost reversal within 1-2 years, especially suitable for large-scale production scenarios. III. Decision Tree for Application Scenarios: How to Select Scientifically? 1.Substrate Hardness: Steel/Titanium Alloy ➔ Ceramic Beads Aluminum Alloy/Plastic ➔ Plastic Beads 2.Process Objectives: High-precision Roughness ➔ Ceramic Beads Deburring/Mild Cleaning ➔ Plastic Beads 3.Compliance Requirements: Export to the EU/Require ESG Report ➔ Ceramic Beads Short-term Internal Projects ➔ Plastic Beads IV. Technological Trends: Why are Ceramic Sandblasting Beads the Future Mainstream? Composite Ceramic Technology: The new ZrO₂ toughened alumina (ZTA) ceramic beads have increased fracture resistance by 300% and have been applied to the treatment of aero-engine blades. Intelligent Adaptation: By using an AI algorithm to match the particle size of ceramic beads with pressure parameters in real time, the yield has increased by 18% (Case: A new energy battery shell manufacturer). Policy-driven: 35% of global manufacturers plan to phase out plastic sandblasting media and switch to ceramic or steel shot solutions by 2025. V. Brand Advantages: Why Choose [HENGLIHONG] Ceramic Sandblasting Beads? Customized Services: Provide full particle size coverage from 80 mesh to 800 mesh, and support customization according to JIS/SAE standards. Quality Assurance System: Promise a crushing rate of less than 0.1% after 100,000 cycles, and provide free sample testing and process optimization solutions. Global Cases: It has reduced the average annual sandblasting cost by 42% and reduced the downtime by 65% for customers such as Bosch and Siemens. Act Now: Visit [www.hlh-js.com] to obtain the "White Paper on the Selection of Sandblasting Media", or make an appointment for a free technical consultation to optimize the ROI of your surface treatment!
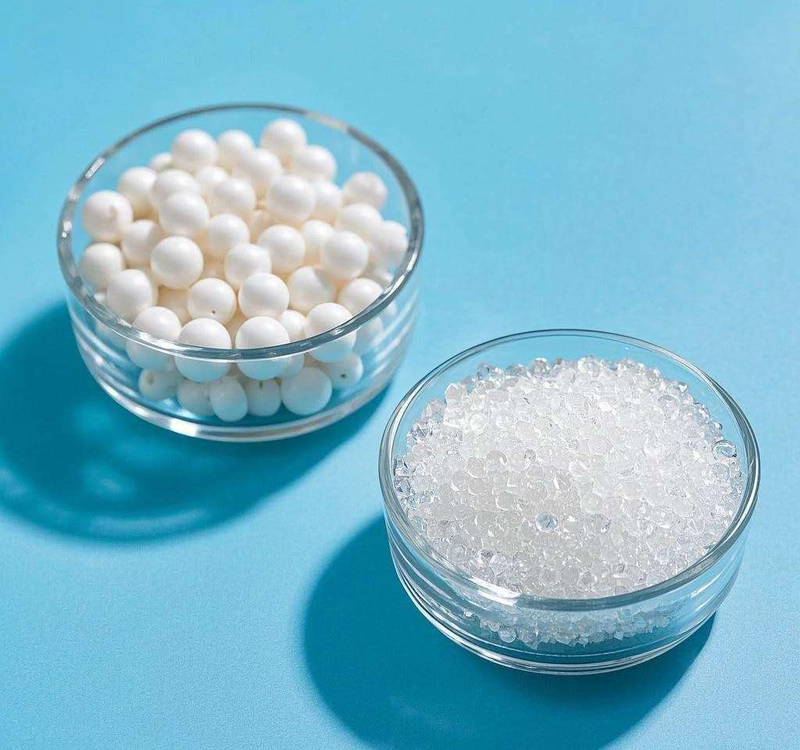
As one of the core processes in the field of surface treatment, sandblasting technology is crucial for material removal efficiency, surface roughness control, and cost optimization. The choice of sandblasting media, especially the comparison between ceramic sandblasting beads and plastic sandblasting beads, has become a key issue in engineers' decision-making. Based on technical parameters, application scenarios, and long-term benefits, this article will analyze the core differences between the two and provide scientific suggestions for selection.
I. Comparative Analysis of Core Performance: Technical Parameters and Process Adaptability
1.Hardness and Wear Resistance
- Ceramic Sandblasting Beads (based on Al₂O₃/ZrO₂): With a hardness as high as Mohs 8-9, they can be reused more than 500-1000 times, showing significant long-term cost benefits.
- Plastic Sandblasting Beads (based on PA/PU): With a hardness of Mohs 2-3, the average lifespan is only 10-50 times. Frequent replacements lead to an increase in implicit costs.
Applicable Scenarios:
Ceramic beads are more suitable for high-intensity continuous operations (such as removing oxidation scale from automotive parts), while plastic beads are suitable for mild surface cleaning of precision electronic components or soft metals (such as aluminum and magnesium alloys) due to their low impact force.
2.Surface Treatment Effects
Roughness Control:
By adjusting the particle size (80-300 mesh), ceramic beads can achieve precise control of Ra 0.5-5μm, with a uniformity error of less than 5%; due to the easy deformation of plastic beads, the roughness fluctuation can reach 20%.
Pollution Risk:
Plastic beads may melt and adhere to the substrate under high-speed impact (especially in working conditions above 80℃), requiring additional cleaning procedures; ceramic beads have strong chemical inertness and no residue risk.
3.Environmental Protection and Compliance
Microplastic Problem: Microplastic particles are generated after the wear of plastic sandblasting beads, facing regulatory restrictions of the EU's REACH and the US EPA, increasing the treatment cost by 30%-50%.
Circular Economy: Ceramic sandblasting beads support 100% recycling and regeneration, meeting the requirements of ISO 14001 certification, and reducing the carbon footprint by more than 60%.
II. Cost Model: Short-term Investment vs. Long-term Returns
Cost Items Ceramic Sandblasting Beads PlasticSandblasting Beads
Initial Unit Price $15-30/kg $5-10/kg
Service Life 500-1000 times 10-50 times
Annual Consumable Cost* $300-600 $2000-5000
Waste Disposal Cost $0 (recyclable) $50-100/ton
*Assuming an annual consumption of 100kg and the equipment operates 300 days a year
Conclusion: Ceramic sandblasting beads can achieve cost reversal within 1-2 years, especially suitable for large-scale production scenarios.
III. Decision Tree for Application Scenarios: How to Select Scientifically?
1.Substrate Hardness:
- Steel/Titanium Alloy ➔ Ceramic Beads
- Aluminum Alloy/Plastic ➔ Plastic Beads
2.Process Objectives:
- High-precision Roughness ➔ Ceramic Beads
- Deburring/Mild Cleaning ➔ Plastic Beads
3.Compliance Requirements:
- Export to the EU/Require ESG Report ➔ Ceramic Beads
- Short-term Internal Projects ➔ Plastic Beads
IV. Technological Trends: Why are Ceramic Sandblasting Beads the Future Mainstream?
Composite Ceramic Technology: The new ZrO₂ toughened alumina (ZTA) ceramic beads have increased fracture resistance by 300% and have been applied to the treatment of aero-engine blades.
- Intelligent Adaptation: By using an AI algorithm to match the particle size of ceramic beads with pressure parameters in real time, the yield has increased by 18% (Case: A new energy battery shell manufacturer).
- Policy-driven: 35% of global manufacturers plan to phase out plastic sandblasting media and switch to ceramic or steel shot solutions by 2025.
V. Brand Advantages: Why Choose [HENGLIHONG] Ceramic Sandblasting Beads?
- Customized Services: Provide full particle size coverage from 80 mesh to 800 mesh, and support customization according to JIS/SAE standards.
- Quality Assurance System: Promise a crushing rate of less than 0.1% after 100,000 cycles, and provide free sample testing and process optimization solutions.
- Global Cases: It has reduced the average annual sandblasting cost by 42% and reduced the downtime by 65% for customers such as Bosch and Siemens.
Act Now:
Visit [www.hlh-js.com] to obtain the "White Paper on the Selection of Sandblasting Media", or make an appointment for a free technical consultation to optimize the ROI of your surface treatment!