5 Steps to Optimize Sandblasting Parameters for 30% Higher Efficiency!
In the machining and aviation manufacturing industries, sandblasting is a core surface treatment process. However, many companies struggle with inefficiency and high costs due to poorly configured sandblasting equipment parameters. This guide provides a step-by-step, actionable approach for engineers and operators to optimize sandblasting efficiency, reduce waste, and improve results. Plus, don’t miss the sandblasting optimization video (linked at the end) for hands-on demonstrations! Step 1: Define Objectives – Identify Key Sandblasting Requirements Keyword Matching: Select parameters based on workpiece material (e.g., aluminum alloy, titanium) and surface finish needs (roughness, cleanliness). Efficiency Trap: Increasing air pressure or abrasive flow too much can accelerate nozzle wear—balance removal rate with equipment longevity. Case Study: An aviation parts manufacturer reduced blasting time by 15% and saved ¥120K/year in consumables after parameter optimization. Step 2: Key Parameter Adjustments – Fine-Tune 5 Critical Variables Air Pressure (PSI) Recommended range for aviation aluminum: 60-90 PSI (too low = poor cleaning, too high = surface damage). Use a digital pressure gauge for real-time calibration. Abrasive Type & Grit Size Aluminum oxide (general use) vs. glass beads (fine polishing)—choose based on application (watch abrasive comparison video). Grit selection: 80-120 mesh for fast paint removal, 220+ mesh for fine textures. Nozzle Size & Shape Larger nozzles (e.g., Φ10mm) increase coverage but require higher pressure. Venturi nozzles improve efficiency by 20-30% over straight-bore nozzles. Blast Angle & Distance Angle: 75°-90° for fast stripping, 45° for uniform texturing. Distance: 150-250mm is optimal (too close = deformation, too far = energy loss). Abrasive Flow Control Adjust via abrasive valve to match air pressure (refer to equipment manual curves). Step 3: Equipment Testing – Validate with Data Record baseline metrics: Time per part, abrasive consumption, surface roughness (Ra). A/B Testing: Adjust one parameter at a time and compare results (e.g., does increasing PSI from 70→80 linearly improve speed?). Recommended tools: Use a roughness tester and digital scale for objective measurements. Step 4: Automation & Monitoring – Ensure Long-Term Stability Install flow sensors and pressure feedback systems for real-time adjustments. Aviation industry case: One company reduced equipment failures by 40% and boosted output by 22% with IoT sensors. Step 5: Regular Maintenance – Protect Your Optimization Gains Weekly: Inspect nozzle wear (replace if diameter expands by >10%). Monthly: Clean recycling system filters to prevent clogging. Annual: Calibrate equipment gauges for accuracy. User Engagement & Video Call-to-Action
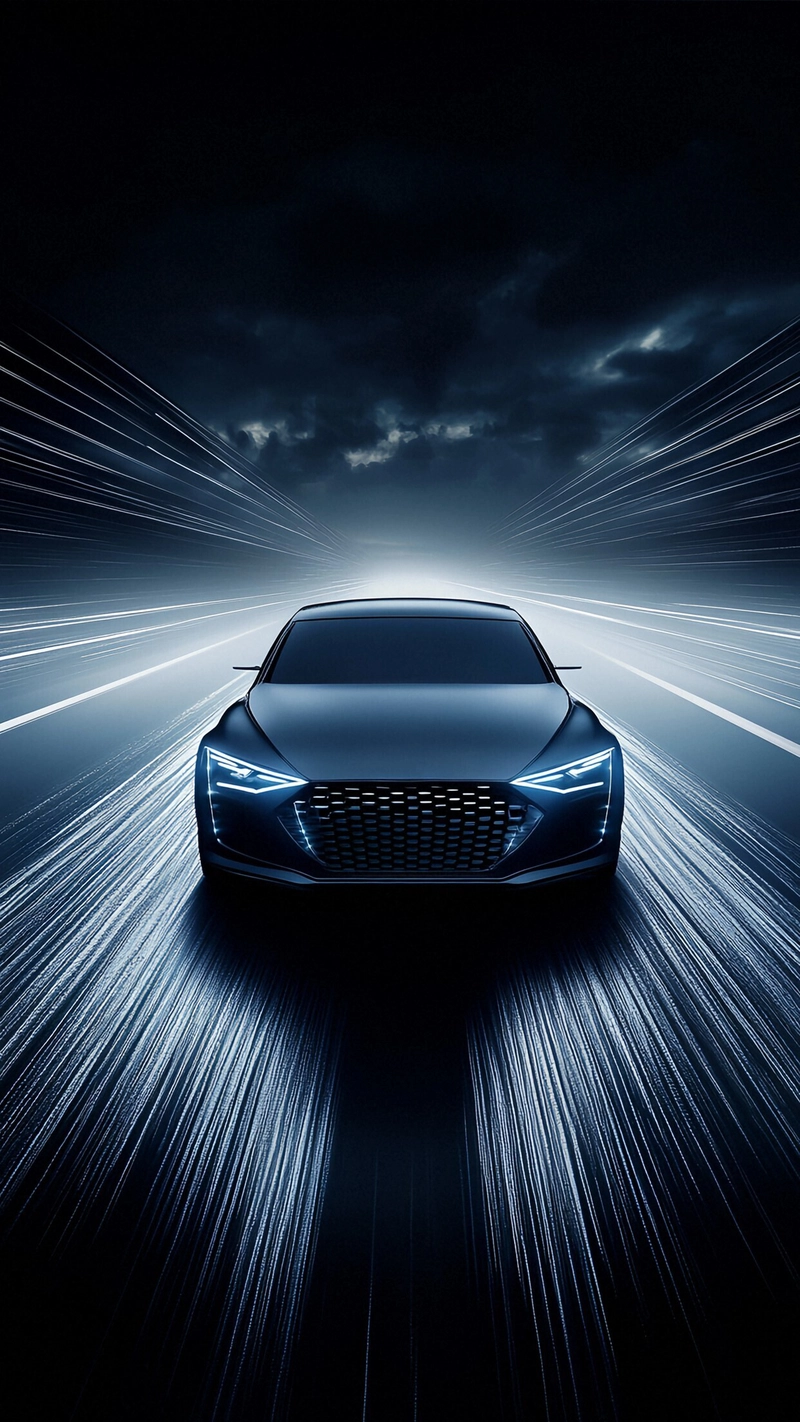
In the machining and aviation manufacturing industries, sandblasting is a core surface treatment process. However, many companies struggle with inefficiency and high costs due to poorly configured sandblasting equipment parameters. This guide provides a step-by-step, actionable approach for engineers and operators to optimize sandblasting efficiency, reduce waste, and improve results. Plus, don’t miss the sandblasting optimization video (linked at the end) for hands-on demonstrations!
Step 1: Define Objectives – Identify Key Sandblasting Requirements
- Keyword Matching: Select parameters based on workpiece material (e.g., aluminum alloy, titanium) and surface finish needs (roughness, cleanliness).
- Efficiency Trap: Increasing air pressure or abrasive flow too much can accelerate nozzle wear—balance removal rate with equipment longevity.
- Case Study: An aviation parts manufacturer reduced blasting time by 15% and saved ¥120K/year in consumables after parameter optimization.
Step 2: Key Parameter Adjustments – Fine-Tune 5 Critical Variables
Air Pressure (PSI)
Recommended range for aviation aluminum: 60-90 PSI (too low = poor cleaning, too high = surface damage).
Use a digital pressure gauge for real-time calibration.
Abrasive Type & Grit Size
Aluminum oxide (general use) vs. glass beads (fine polishing)—choose based on application (watch abrasive comparison video).
Grit selection: 80-120 mesh for fast paint removal, 220+ mesh for fine textures.
Nozzle Size & Shape
Larger nozzles (e.g., Φ10mm) increase coverage but require higher pressure.
Venturi nozzles improve efficiency by 20-30% over straight-bore nozzles.
Blast Angle & Distance
Angle: 75°-90° for fast stripping, 45° for uniform texturing.
Distance: 150-250mm is optimal (too close = deformation, too far = energy loss).
Abrasive Flow Control
Adjust via abrasive valve to match air pressure (refer to equipment manual curves).
Step 3: Equipment Testing – Validate with Data
Record baseline metrics: Time per part, abrasive consumption, surface roughness (Ra).
A/B Testing: Adjust one parameter at a time and compare results (e.g., does increasing PSI from 70→80 linearly improve speed?).
Recommended tools: Use a roughness tester and digital scale for objective measurements.
Step 4: Automation & Monitoring – Ensure Long-Term Stability
Install flow sensors and pressure feedback systems for real-time adjustments.
Aviation industry case: One company reduced equipment failures by 40% and boosted output by 22% with IoT sensors.
Step 5: Regular Maintenance – Protect Your Optimization Gains
Weekly: Inspect nozzle wear (replace if diameter expands by >10%).
Monthly: Clean recycling system filters to prevent clogging.
Annual: Calibrate equipment gauges for accuracy.
User Engagement & Video Call-to-Action